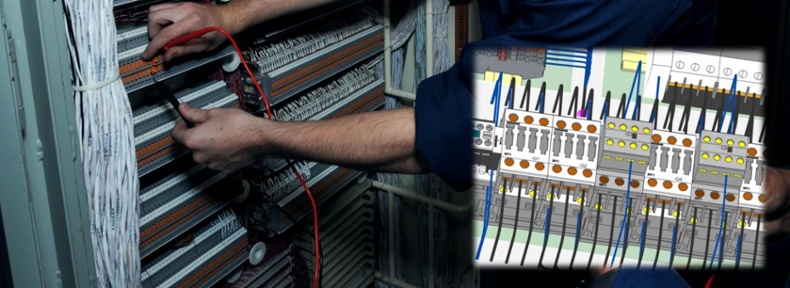
Optimizando el Tablero de Mando para Maquinas Industriales
Incrementada eficiencia del controlador de motor, productividad mejorada y coste mejorado de expulsado son algunos de los principales cambios por los que luchan las empresas a través de la optimización de los cuadros de mandos eléctricos. Los proyectistas y los ingenieros de cuadros de mando se concentran en retos involucrados en los diseños corrientes con el fin de usar le mejor rendimiento posible. Estos retos tratan con el empleo ambiental, el coste de seguridad, las cuestiones de ruido de interferencia electromagnética, y la optimización del espacio del cuadro de mando.
Los proyectistas y los ingenieros tienen restricciones de tiempo limitado para terminar los planos de los cuadros de mando y, no pocas veces, encuentran problemas para que se produzcan productos con un ciclo de vida robusto y que también cumpla con todos los requisitos de proyecto. Los productos no se repiten idealmente en ambientes extremos como lo hacen en ambientes controlados. Cuestiones prácticas, probadas en campo, pueden conllevar la necesidad de tiempo de parada para que sean reparados los sistemas dañados, lo que puede resultar en mantenimiento costoso.
El artículo se profundizará en soluciones y prácticas que ayudan a los ingenieros de controles y a los proyectistas de cuadros optimizar el desarrollo de cuadros de mando y el ciclo de vida del producto. Ello proporcionará sugerencias y herramientas para que se produzcan mejores soluciones de proceso con el objeto de reducir el coste y mejorar el rendimiento del ciclo de vida.
Optimización del Espacio del Cuadro de Mandos
Los ingenieros y proyectistas de máquinas son desafiados a reducir constantemente e tamaño y la huella de las máquinas que construyen. Eso significa que los proyectistas necesitan construir huellas menores para abrigar más en los cuadros de mando existentes. Maximizar el espacio de la plataforma de la caja es una buena solución. Pero hay varios retos en proyectar cuadros de mando menores. Las consideraciones incluyen:
- Segregación de Cables
- Gestión Térmica
- Entrada de Cables
- Interferencia Electromagnética
- Radio de Curvatura de Cable
- Espacio para Expansión Futura
Aparte de las cuestiones de seguridad, la conformidad con los estándares y códigos, así como la obediencia a los requisitos de separación de componentes electrónicos, dejan los trabajos del ingeniero u del proyectista ese tanto más complicados.
Los cuadros de mando remontan a la caja de control tradicional y al diseño de una sola puerta. Los cuadros de mando tienen mucho más versatilidad, con cajas de paneles diseñadas con puntos de acceso múltiples, compartimientos abajo del panel y sistemas opcionales de enfriamiento integrados. Un área que muchos tienden a no usar es el espacio entre la puerta del gabinete y los componentes montados en el sub-panel, en la parte de atrás. Usar rieles DIN, con componentes que serían normalmente instalados en el sub-panel.
Con sistemas de enfriamiento integrados, los paneles de control pueden permitir que equipos eléctricos sean montados e instalados más cerca uno del otro. Eso reduce el espacio usado y mejora la eficiencia de disipación del calor dentro de la unidad. Hay una abundancia de sistemas de enfriamiento disponibles y escoger el sistema cierto depende de las necesidades del panel de control.
Mitigación de Ruido
La interferencia electromagnética de componentes externos emite ruido que puede finalmente interferir en las operaciones normales de otros componentes. El riesgo de IEM aumenta con la adición de componentes conectados en red y aparatos de potencia mientras se minimizan los costes del panel. Es difícil detectar componentes emisores de ruido una vez que está completo el panel de control; luego, para reducir las chances de una posible IEM, incorporar soluciones de mitigación de ruido en el proyecto original es esencial.
La adecuada conexión a tierra de los componentes emisores de ruido constituye un gran primer paso en la reducción de las emisiones de IEM. Cables que forman bucles producen excelentes antenas y la acción de minimizar el tamaño de los bucles ayudará a reducir el ruido recibido. En lugar de lazar cables, pase cables de alimentación y retorno juntos. La acción de torcer cables juntos reduce los efectos de la IEM aún más. Una los conductores de tierra de entrada con el sub-panel por donde entran, usando una barra de tierra universal.
La distribución de cables es una consideración crucial en el control de ruido y la distancia entre los dos es un grande factor a lo largo de la distribución del circuito de cables. Cruce los cables conductores a ángulos correctos, a la vez que conductores perpendiculares tienen mucho menos longitud en común que los conductores paralelos, reduciendo de esta manera el ruido. Evite pasar corriente continua cerca de corriente alterna - y salidas cerca de entradas. Para reducir la IEM, se recomienda una distancia de 3 a 6 pulgadas [7,62 a 15,24 cm] entre los conductores de alta tensión y de baja tensión en cursos paralelos. Y se recomienda 12 pulgadas [30,48 cm] entre los cables de retorno de solucionadores y de codificadores, y cualesquiera cables de energía en corriente alterna o motor.